Scrap In
The Scrap In transaction is used to manage item movement from the Formulatrix scrap warehouses in bonded zones (PSL & PSM) to non-bonded areas. This way, the transaction will not be classified as an export. The “scrap” items involved are not necessarily damaged, unusable, or waste. In some cases, these are functional items moved for reasons such as subcontracting, intercompany transfers, or vendor returns. The “Warehouse” team tracks and manages these items to ensure that inventory records are accurate and compliant with regulations. Through this process, Scrap In serves the following purposes:
Intercompany Order
Scrap In is used to move usable goods from PSL or PSM scrap warehouses to FOR warehouse for replenishment and fulfillment. For example, the Machining division at FOR needs a storage rack and PSL has one. After completing the WO & PO process, this item can be moved to FOR using the Scrap In transaction.
Return to Vendor
When an item arrives and fails quality control (QC) checks, the Accounting team performs an Adjustment Move Out transaction to transfer it to the scrap warehouse. The Scrap In transaction is then used to record the item for return to the vendor.
Sale of Scrap Materials
Scrap In is used for selling leftover materials to scrap sales vendors. The items include scrap wire, acrylic, or plastic, as well as OTS (Order to Stock) items like screws or parts.
Store Unusable or Damaged Items
Use Scrap In to store items that are no longer functional or have expired within the company.
Scrap In Process
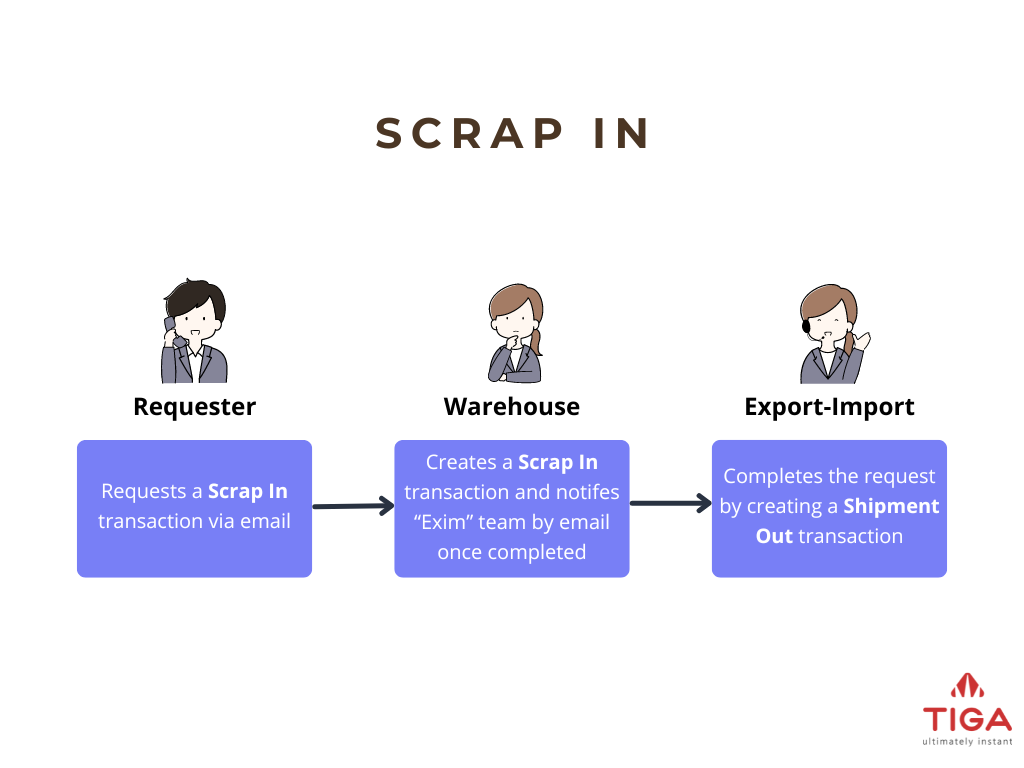
Scrap In Process
Receiving the Request
Processing the Request
Upon receiving the request, the “Warehouse” team creates a Scrap In record, including Transaction Line Items (TALI) for each item. Once done, they will inform the requester and “Exim” via email that the record has been created.
Completing the Request
The “Exim” team completes the process by creating a Shipment Out record to move the items out of the scraps warehouse.
Related Topics: